Internet of Things in Manufacturing
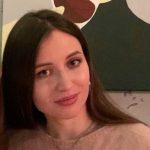
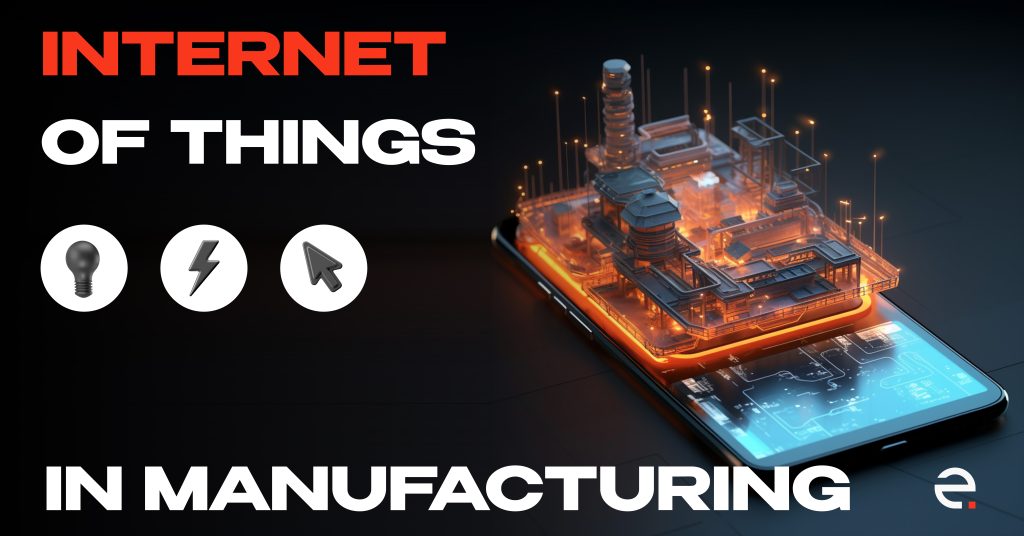
Nowadays, the widespread incorporation of IoT into manufacturing operations has reached unprecedented levels. The Industrial Internet of Things (IIoT) is reshaping conventional factories. We see how intelligent and interconnected environments are revolutionizing the entire production landscape. As businesses across the industry increasingly grasp the advantages of IIoT, its implementation is projected to expand even further in the forthcoming years.
Today, we discuss the significance of IoT in manufacturing. Keep on reading to uncover why embracing the technology is a vital step for your facility!
The Importance of IoT in Manufacturing
Let’s delve into the profound influence of IoT technology in general. Over the past few years, this industry has witnessed an unprecedented surge. The advent of widespread internet connectivity has facilitated the integration of various devices into a cohesive ecosystem. From smart home solutions to innovative wearables, the range of possibilities keeps expanding. According to THIS report, the number of IoT-connected devices will exceed a staggering 75 billion by 2025.
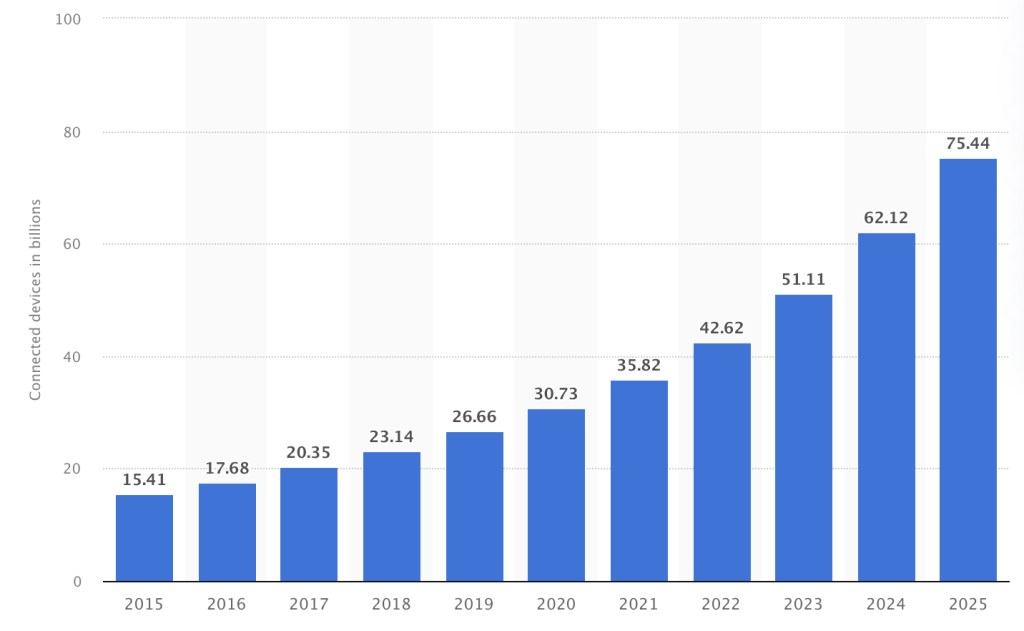
Now, let’s explore possibilities of IoT for manufacturing. In two words, this transformative technology empowers companies to optimize their production processes. But what exactly could manufacturers expect if they decide to harness its power? Let’s explore main benefits in detail:
Enhancing Efficiency and Productivity
IoT-enabled devices have emerged as game-changers in the industry. They seamlessly gather real-time data from equipment spread across the manufacturing floor. Therefore, companies quickly identify and address problem areas. They can optimize processes and streamline overall operations based on real-time data. It minimizes downtime, plus, there is no need for frequent manual intervention.
Reducing Operating Costs
Manufacturers have got access to real-time analytics and predictive maintenance capabilities. Instead of fixed schedules, they plan maintenance activities based on current equipment condition. Plus, manufacturers accurately foresee potential failures and plan mandatory activities well in advance. This forward-thinking approach serves two crucial purposes:
1) it helps manufacturers steer clear of costly unplanned downtime;
2) It decreases the likelihood of expensive repairs.
Additionally, such sensors can track energy consumption. Thus, they help companies identify areas for optimization and implement energy-saving initiatives.
Enhancing Quality Control
Keeping proper quality level is vital for the production industry. Even minor defects lead to product recalls and damage to brand reputation. With real-time monitoring, manufacturers track data at every stage of the production process.
Automated sensors measure various parameters (temperature, humidity, etc). Thus, it ensures that products meet strict standards. Any anomalies or deviations from specified parameters can be immediately detected.
Ensuring Worker Safety
Ensuring the safety of staff remains an utmost priority within any facility. The IoT technology integration has emerged as a crucial component in creating a secure working environment. IoT-enabled sensors monitor various factors such as temperature, air quality, and noise levels. Thus, workers and supervisors are promptly alerted to any unsafe conditions that arise. By continuously monitoring and analyzing these conditions, potential hazards can be swiftly identified.
IoT Applications in Manufacturing
The technology is transforming traditional production methods into smart and efficient systems. Thanks to:
Real-Time Monitoring
By deploying sensors on critical equipment, manufacturers can monitor various parameters. These may include temperature, vibration, energy consumption, and more. Any detected anomalies trigger alerts. Thus, operators take immediate action before a breakdown occurs.
Predictive Maintenance
Traditional maintenance practices are often reactive, leading to unexpected breakdowns and costly repairs. IoT-enabled sensors help forecast when equipment or machinery is likely to fail. By monitoring the performance of machines, algorithms detect warning signs of potential failures. This allows manufacturers to schedule maintenance activities before a problem occurs.
Asset Tracking and Inventory Management
By tagging assets/products with connected sensors, manufacturers can track their location, status, and movement. This level of visibility enables precise inventory management. The number of stockouts/overstocking cases and manual errors decrease. It also improves supply chain efficiency. How? By providing accurate tracking info throughout the production process!
Smart Factories
IoT technologies transform traditional manufacturing into a highly connected and automated environment. It becomes a modern unified ecosystem. Machines communicate with each other, automatically adjusting production parameters, based on real-time demand and quality requirements. Smart factories leverage such autonomous systems to enhance accuracy in tasks such as:
- assembly
- packaging
- logistics and more.
Challenges of IIoT Adoption and How to Overcome Them
With its promise of increased productivity, companies are eager to adopt the technology. However, like any major technological shift, there are several challenges they should consider:
Security Concerns
With an increasing number of connected devices, the risk of cyber attacks and data breaches becomes more significant. Robust security measures in place help protect sensitive data and prevent unauthorized access. Here is a short action plan:
- Start by assessing the potential risks and vulnerabilities in your system. Identify potential attack vectors, weak points in the network, etc.
- Secure network connections by using encrypted protocols such as HTTPS or TLS.
- Implement firewalls and intrusion detection systems to detect and prevent unauthorized access.
- Choose role-based access control. Grant different access levels based on job roles and responsibilities.
- Utilize robust monitoring tools to detect abnormal behavior or anomalies in the system.
Interoperability Issues
In manufacturing, we speak about the integration of various sensors, machines, and platforms. Legacy systems often employ outdated communication protocols that are incompatible with newer technologies. This disparity makes it challenging for devices to interpret data exchanged between them. Plus, their integration with IoT devices may require investments in hardware/software solutions. This may be costly and time-consuming. Especially, if manufacturers need to retrofit existing infrastructure to accommodate new technologies. What’s your action plan?
- Embracing standardized communication protocols facilitates seamless integration across different devices and platforms. MQTT or OPC UA standards provide a common language for devices to exchange data;
- Implementing middleware solutions also simplifies the integration process. Think about message brokers or service-oriented architectures;
- Use APIs that abstract complex data formats and provide standardized interfaces.
- Instead of entirely replacing legacy systems, adopt a phased approach to integration. This allows for gradual migration, ensuring a smooth transition to interoperable systems.
Scalability and Reliability
Scaling up an IoT infrastructure may be a complex task. Issues such as latency, bandwidth limitations, and device compatibility may arise. So, how to ensure this scalability?
- Design a network architecture that can handle the increased number of devices and data traffic. Consider using a combination of wired and wireless technologies. It will ensure reliable connectivity throughout the facility.
- Choose a cloud platform that can accommodate the growing demands of your IoT infrastructure. Look for features like auto-scaling and load balancing to handle increased data processing requirements.
- Implement redundancy and failover mechanisms to ensure uninterrupted operation of critical IoT components. This includes:
- redundant servers
- backup power supplies
- duplicate communication channels.
They all help mitigate any single point of failure.
- Set up a scalable data storage and processing system. Consider using distributed databases or data lakes that may handle large data volumes.
- Conduct thorough testing and validation before scaling up the infrastructure.
Before completing these steps, consult with experts specializing in iot solutions for manufacturing.
Developing a IoT Solution for Manufacturing
Embarking on an IoT journey may be a complex and daunting task. To ensure a successful implementation, it is crucial to have a clear plan and strategy in place. Let’s explore the key steps you need to take here to achieve an expected outcome:
Identify the Key Objectives
Define your goals to determine the specific functionalities required for your solution. Key objectives may include:
- improving quality control
- optimizing inventory management
- increasing overall equipment effectiveness etc.
Determine the Scope of the Solution
Identify the devices, sensors, and machines that need to be connected to the network. Consider factors such as:
- type of data needed
- communication protocols required
- infrastructure needed to support your solution etc.
Select the Right IoT Platform
A platform acts as the backbone of your solution. It enables you to collect, analyze, and visualize generated data. How to choose the right option?
1) Ensure the platform can scale and support devices/systems you plan to implement.
2) Assess its security measures. Look for compliance with industry standards.
3) Evaluate data analytics capabilities.
4) Consider how easy it is to integrate the platform with your existing systems.
5) Determine if the platform allows for customization to tailor it to your processes.
6) Clarify data ownership and privacy policies. Make sure data remains under your control and complies with relevant regulations.
Then, deploy sensors and connect devices to the network to start receiving data. How to ensure its accuracy and consistency? Apply preprocessing techniques, such as cleaning, normalization, and data enrichment.
Implement Proper Analytics
Uncover patterns, trends, and insights within the collected data. ML or statistical analysis will help you to get the most accurate results. Plus, think about convenient visualization and reporting. And, most importantly, act upon derived insights!
Ensure Security
Robust security measures will help protect your solution from cyber threats. This includes:
- encrypting data
- securing communication channels
- training your staff etc.
Build Your IoT Solution in Manufacturing with Ein-des-ein
Our team is well-equipped to tackle even complex projects in the manufacturing domain. We will help you implement real-time tracking capabilities in your operations. Ein-des-ein’s commitment to excellence has earned us recognition in the industry. We have been featured as a top app development company in the USA and Poland. Our expertise has also been acknowledged by The Manifest. Choosing Ein-des-ein means cooperating with a reputable and trusted partner.
FAQ
-
How to implement IoT in manufacturing?
-
At first sight, IoT and manufacturing seem to be non-connectable. But, the implementation process is not that scary and complicated as you may think! Here are steps you should follow to implement internet of things in manufacturing:
- Determine the specific objectives you want to achieve through this implementation. Evaluate your existing infrastructure and equipment. It will help you to identify areas where the technology could make the most impact.
- Choose a reliable platform. It should align with your requirements and support integration with existing systems.
- Implement robust cybersecurity measures. Provide comprehensive training to your employees.
-
Does your company have any experience in implementing IoT solutions in other industries?
-
Absolutely! For example, our company worked on a remote patient monitoring system for a healthcare organization. Patients were provided with wearables, such as smartwatches or health trackers. These wearables monitored vital signs like heart rate or oxygen levels.
Real-time alerts were generated when the system detected any deviations from normal health ranges. These alerts were sent to both the patient’s smartphone and the healthcare provider’s dashboard. It ensured immediate attention and intervention if necessary.
We also worked on a mobile app for a smart home startup. Firstly, we developed a user-friendly interface. It allowed homeowners to control various aspects of their smart homes. Next, we integrated the app with compatible smart devices.
We also implemented a scheduling feature. Homeowners could automate routines based on their preferences. They’d set the lights to turn on at a specific time or adjust the thermostat before arriving home.
To enhance security, we added a robust authentication system. Only authorized users could access and control the features. Additionally, we integrated real-time notifications. They alerted homeowners of any unusual activity.
We also incorporated energy management capabilities into the application.
For convenience, we included voice control functionality. Users could activate and control various features using voice commands.